
Adherence to the lamination pressure standards with optimum heating and cooling cycle profiles, using a high-performance press, Figure 2.Įlectrical Tests Provide Confidence, Assurance, Regulatory AdherenceĮven a basic component such as laminated bus bar needs multiple electrical tests to verify there are no material, manufacturing, or latent defects.Precise alignment and interconnection of multiple layers, maintaining minimum creepage and clearance dimensions.Planarity of the individual metal layers.It’s the attention to small but critical details that assures a high-performance laminated bus bar with consistent long-term performance and reliability.
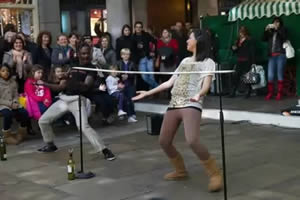
Manufacturing, Fabrication Expertise Also Criticalĭespite the simple concept of the laminated bus bar, manufacturing a reliable, quality component requires experience with respect to obvious and not-obvious issues. Of course, the design and fabrication must also meet multiple safety and performance standards, including creepage (over surface) and clearance (through air) requirements for the intended operating voltage.
#ELECTRIC LIMBO BAR PC#
Short, lower-capacity laminations can be easily manufactured for small- and medium-size PC boards and circuits that only need to handle the lower power levels and have few spacing or installation constraints. Laminated bus bars can be designed with wide range of sizes and configurations. However, designing and fabricating a laminated bus bar that meets project requirements and has short- and long-term reliability requires expertise, skills, attention to detail, and careful testing. These bus bars are a clean, clear, and direct mechanical solution to a problem defined by electrical engineering realities, and can even provide some relief to heat-dissipation issues.ĭesigns Driven by Each Customer’s Unique NeedsĪt first look, laminated bus bars appear to be fairly basic mechanical assemblies made up from only a few distinct parts, with little complexity in design and needing only a few final assembly steps.

Depending on size and thickness, laminated bus bars can support voltages and currents ranging from low, single-digit values up to hundreds of volts and amps and even higher. Laminated bus bars address two power-related design challenges: they significantly reduce voltage drop due to IR loss in high-current power-distribution systems, and their very low stray inductance minimizes a possible cause of instability and output oscillation in switching power supplies.
